When selecting a motor for a precision control application, engineers often debate between two popular options: servo motors vs stepper motors. Each motor type has distinct characteristics that make it better suited for specific tasks. In this servo vs stepper motor technical guide, we will dive deep into their design, performance, advantages, and real-world pros and cons based on user experiences.
Understanding Stepper Motors
Stepper motors are electromechanical devices that move in discrete steps. They are controlled by sending pulses to the motor driver, each pulse rotating the motor shaft by a fixed angle.
Stepper motors are rotary actuators that move in discrete steps. They consist of a rotor with multiple teeth or poles and a stator with electromagnets. By sequentially energizing the electromagnets, the rotor is forced to rotate in steps, allowing for precise control over the angular position.
Construction: Multiple coils organized in phases.
Movement: Precise steps (typically 1.8° per step, or 200 steps per full rotation).
Control: Open-loop (no feedback from the motor).
Typical Applications:
- 3D printers
- CNC machines
- Camera platforms
- Plotters
Understanding Servo Motors
Servo motors are closed-loop systems that combine a motor with a feedback sensor (such as an encoder). The system continuously adjusts the motor’s performance based on real-time feedback to achieve the desired position or speed.
Construction: DC or AC motor + encoder/sensor + controller.
Movement: Smooth, continuous rotation or precise angular position control.
Control: Closed-loop (with feedback).
Typical Applications:
- Robotics
- High-speed CNC machines
- Industrial automation
- Drones and aerospace
Servo Motors vs Stepper Motors: Key Technical Comparisons
Feature | Stepper Motor | Servo Motor |
---|---|---|
Control Type | Open-loop | Closed-loop |
Accuracy | High (in low-speed, low-load situations) | Very High (with feedback correction) |
Speed | Moderate | High |
Torque at Low Speed | High | Moderate (but adjustable with gearing) |
Torque at High Speed | Drops significantly | Maintains high torque |
Cost | Lower | Higher |
Complexity | Simple system | More complex (requires controller + sensor) |
Efficiency | Lower (especially when holding position) | Higher |
Heat Generation | High (always energized) | Lower (only energized as needed) |
Reliability | Very reliable in simple systems | Very reliable with proper tuning |
Best Motor for Precision Control
If your project demands extreme precision, speed, and adaptability, servo motors are usually the best motor for precision control. Thanks to their feedback loop, they can correct any positioning error almost instantly. On the other hand, for projects with simpler needs, lower speeds, and where budget constraints exist, stepper motors still offer a very high degree of precision and are often the preferred choice.
Types of Steppers Motor
Stepper motors are classified based on their phase configuration and the degree of rotation per step. Here’s a breakdown of the common types:
Unipolar Stepper Motors:
These motors have a single winding per phase. Each winding is connected to a single power supply terminal. Unipolar stepper motors typically utilize a six-wire configuration. Each phase winding has a center tap. These center taps are commonly connected to the motor’s voltage supply (VM). The remaining four wires connect to the motor windings at points A, B, C, and D. Unipolar stepper motors are generally simpler to drive but may require more complex drive circuitry.
Bipolar Stepper Motors:
These motors have two windings per phase, connected in series, and typically two-phase, four-wire devices. Each winding can be energized in either direction, providing more precise control and higher torque compared to unipolar motors. They consist of two primary components: the stator and the rotor.
By Degree:
- Full-Step Mode: In full-step drive mode, the stepper motor driver energizes the two coils of a two-phase stepper motor sequentially based on pulse and direction commands. Each pulse results in a rotational movement of the motor’s rotor by a fixed step angle. The current waveform in this mode is characterized by four distinct states, dividing the circle into four equal parts. This simplicity in current flow, however, leads to rougher motor operation at low speeds, accompanied by increased noise. Despite these limitations, full-step drive offers the advantage of relatively simple hardware and software implementation, making it cost-effective to manufacture.
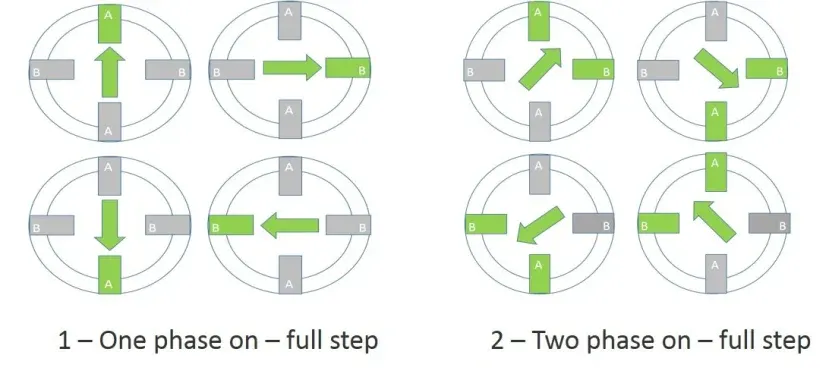
- Half-Step Mode: Half-step excitation mode combines full-step excitation with energizing both phases simultaneously. This results in a step angle that is half the size of the full-step angle, leading to smoother operation due to increased angular resolution. While half-stepping generally results in a 15% torque reduction compared to full-step operation with both phases energized, modified half-stepping techniques can mitigate this by increasing the current applied to the motor during single-phase excitation.
Microstepping Mode: Microstepping significantly enhances the resolution of stepper motor operation by dividing the basic step into up to 256 smaller increments. This technique employs two sinusoidal current waveforms, phase-shifted by 90 degrees, to drive the motor. This approach enables smooth and near-silent operation with minimal detectable stepping action. By precisely controlling the direction and amplitude of current flow in each winding, microstepping improves motor characteristics, reducing vibration and enhancing smoothness. The smooth transition between windings, facilitated by the coordinated increase and decrease of current, maintains consistent torque output. While microstepping enhances resolution and smoothness, it requires more sophisticated driver circuitry to control current levels in each winding and typically results in reduced torque and potentially lower accuracy.
Servo Motors
Servo motors are rotary actuators renowned for their precision in achieving and maintaining desired angular positions. Unlike conventional motors that simply rotate continuously, servo motors incorporate a closed-loop control system that enables them to move to a specific position and hold it steadily. A key component of this system in Servo vs stepper motor technical guide is a feedback mechanism, typically a potentiometer, which continuously measures the actual angular position of the motor’s shaft. This measured position is then compared to the desired position, as determined by the input signal.
Any discrepancy between these two values constitutes an error. The servo’s internal control circuitry, often employing proportional-integral-derivative (PID) control algorithms, analyzes this error and adjusts the motor’s current accordingly to drive the shaft towards the desired position.
This continuous feedback and adjustment process ensures that the servo motor achieves and maintains the specified position with high accuracy, even in the presence of external disturbances.
Any motor that has a closed-loop feedback device that responds to disturbances in the motion profile classifies as a Servo Motor.
Servo motors are primarily classified into two types: Rotary and Linear. Rotary servo motors, the most common type, exhibit rotational motion. This category encompasses various subtypes, including AC servo motors, stepper servo motors, brush DC servo motors, permanent magnet synchronous servo motors, and brushless DC Servo motors.
While rotary motion is inherent to these servos, linear motion can be achieved through mechanical means such as screw threads (ball screws or lead screws) or by employing belts and pulleys.
In contrast, linear servo motors are designed for direct linear motion. They feature a unique configuration where the rotor is positioned within a moveable U-shaped channel, with the coils situated externally.
Which one is most accurate?
As mentioned earlier in Servo motors vs stepper motors, servo motors are typically more accurate than stepper motors. However, there are some applications where stepper motors may be a better choice. For example, if you need a motor that is very fast or very powerful, then a stepper motor may be a better option.
Torque
Servo motors typically have higher torque than stepper motors. This is because they have a larger motor and a more powerful gearbox.
Accuracy
One of the key differences between servo motors and stepper motors is their accuracy. Servo motors are typically more accurate than stepper motors. This is because servo motors use a feedback loop to ensure that they are positioned correctly, while stepper motors do not.
Speed
Stepper motors are typically faster than servo motors. This is because they do not have to wait for a feedback loop to confirm their position.
Cost
Servo motors are typically more expensive than stepper motors. This is because they are more complex to manufacture.
Stepper Motors
Detailed Motor control systems: (Based on User Experiences)
Pros:
Affordable and readily available: Great for hobbyists and prototyping.
Simple to control: Minimal electronics and straightforward setup.
Excellent for low-speed, high-precision tasks: No need for feedback systems.
High holding torque at standstill: Useful for positioning applications.
Cons:
Missed steps under heavy loads: Can lose position without warning.
Reduced torque at high speeds: Not ideal for fast-moving applications.
Heat generation: They often stay powered even when stationary.
No feedback: Cannot correct errors without an external encoder.
- Limited Speed: The step-by-step motion can limit the maximum achievable speed.
Resonance Issues: Stepper motors inherently exhibit slight vibrations with each step due to the rotor’s inertia. This inertia can cause the motor to overshoot or undershoot the desired step position, resulting in oscillations around the target angle. If the frequency of these oscillations aligns with the motor’s natural resonant frequency, resonance occurs. This resonance phenomenon manifests as audible noise, increased vibration, and, in severe cases, can lead to lost steps or complete motor stalling.
Here’s some recommended method to reduce stepper motor resonance:
1. Reduce step size
2. Add damping
3. Use a gearbox
4. Use a chopper drive
Servo Motors
Pros:
High precision with feedback: Always knows and adjusts its position.
High torque at all speeds: Ideal for dynamic and fast applications.
Efficient operation: Draws only the necessary amount of current.
Smooth motion control: Perfect for high-end robotics and automation.
Cons:
Higher cost: Initial investment in motor, driver, and encoder.
More complex setup: Requires careful tuning of control parameters.
Potential for overshooting or instability: If not tuned correctly.
Conclusion:
Choosing between servo motors vs stepper motors ultimately depends on your project’s requirements. For budget-friendly, simple, and moderately precise needs, stepper motors remain a fantastic solution. However, if you demand the best motor for precision control — especially in dynamic, high-speed environments — servo motors clearly outperform.
In any serious servo vs stepper motor technical guide, it’s essential to stress that understanding your specific application needs (speed, load, precision, and cost) is the real key to making the right decision.
FAQ:
- Which is better, servo motors or stepper motors?
It depends on your application—servo motors excel in high-speed, high-torque tasks, while stepper motors are better for precise positioning at lower speeds. - Do servo motors have more torque than stepper motors?
Yes, servo motors typically deliver higher torque at high speeds compared to stepper motors, making them ideal for dynamic applications.
See Also:
Comparison of the Latest Arduino and Raspberry Pi Models and Their Applications